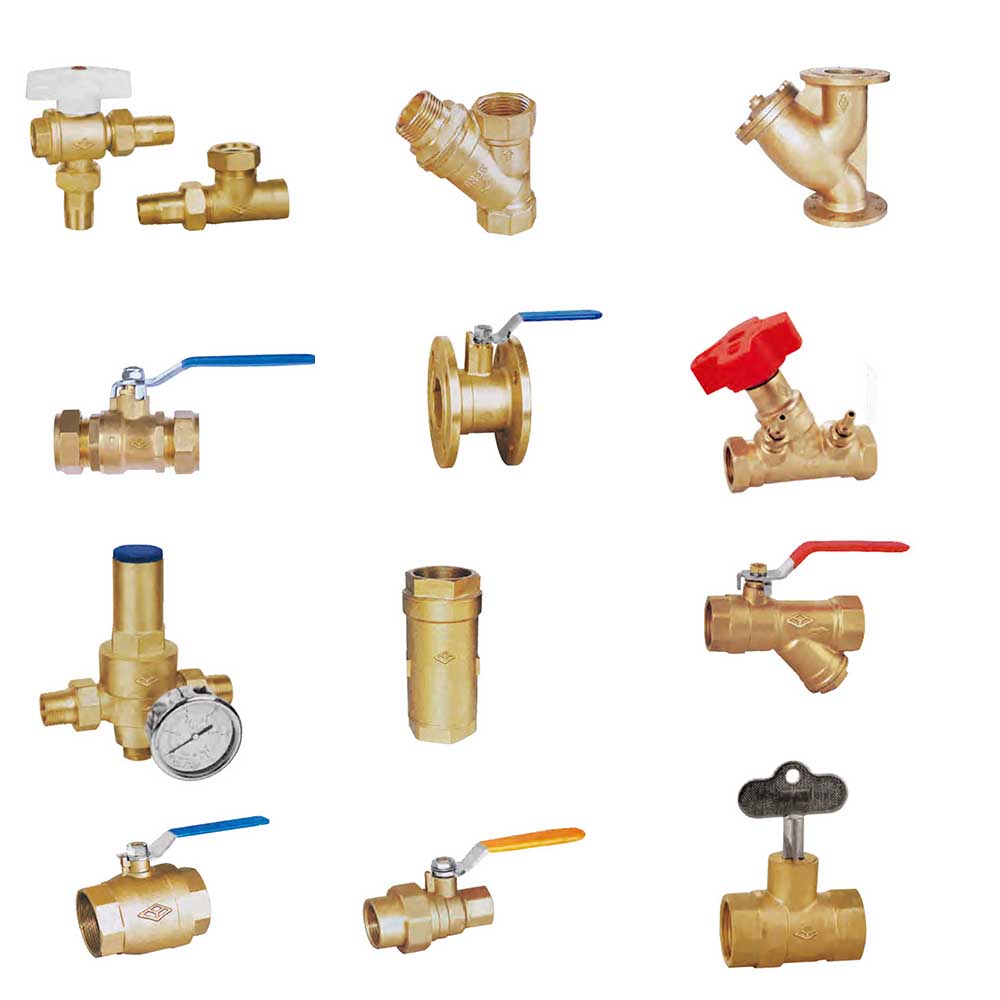
Types of Brass Valve
- Brass Gate Valve
- Brass Ball Valve
- Brass Butterfly Valve
- Brass Check Valve
Brass valves also have the advantage of excellent processing performance, which allows for easy cutting, welding, and other processing, making it easy to produce complex shaped parts. These characteristics together constitute the core advantage of brass valves, making them stand out among numerous valve materials.
Brass valve is a type of valve made mainly of brass, which has unique physical and chemical properties. This type of valve is renowned for its excellent mechanical performance and outstanding corrosion resistance, and is widely used in various industrial and civilian fields. A significant feature of brass valves is their excellent thermal conductivity, which makes them perform well in scenarios that require rapid heat dissipation or insulation.
Brass Gate Valve
Brass Globe Valve
Brass Ball Valve
Brass Butterfly Valve
Brass Check Valve
How to choose the right brass valve?
Brass Valve Type | Characteristic | Application |
Brass Ball Valve | Проста структура, flexible operation | Quick fluid switching |
Brass Globe Valve | Добро уплътнение, high adjustment accuracy | Precise flow control |
Brass Gate Valve | Fast switching speed, suitable for large flow | High-pressure steam system |
Brass Butterfly Valve | Small size, леко тегло | Large-diameter pipeline system |
Brass Material Analysis
Material selection plays a vital role in the design and manufacture of brass valves. The unique composition and performance characteristics of brass alloys directly affect the function and life of the valve. This section will detail the composition and performance characteristics of common materials for brass valves.
Brass valves mainly use copper-zinc alloy as the base material, and the most common grades include H68 and HPb59-1. These alloys achieve excellent mechanical properties and corrosion resistance through carefully designed composition ratios, making them ideal for valve manufacturing.
- H68 brass is known for its excellent plasticity and corrosion resistance, and is suitable for manufacturing valve parts with complex shapes;
- HPb59-1 brass has more advantages in processing performance and wear resistance, and is particularly suitable for manufacturing valve parts that require precision processing and long-term use.
H68 Brass Material Valve
The chemical composition of H68 brass mainly includes:
- Copper: 67.0~70.0%
- Zinc: trace
This alloy exhibits excellent mechanical properties:
- Tensile strength: up to 320MPa
- Elongation: до 55%
The outstanding features of H68 brass include:
- Good plasticity: suitable for complex cold stamping and deep drawing processing
- Excellent corrosion resistance: especially suitable for manufacturing radiator housings and ducts and other parts
- Excellent thermal conductivity: helps valves dissipate heat under high temperature conditions
HPb59-1 Brass Material Valve
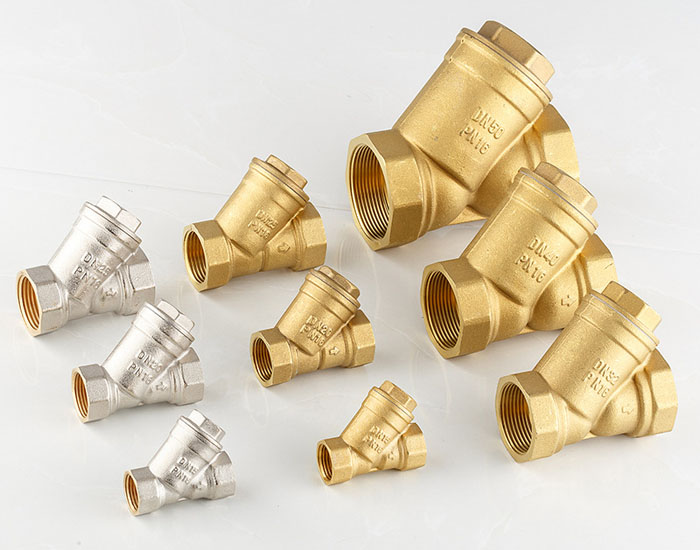
HPb59-1 brass adds trace lead (0.8\~1.9%) on the basis of H68, further improving the processing performance. Typical mechanical properties of this alloy are as follows:
- Tensile strength: 650MPa
- Brinell hardness: HRB 140
The outstanding features of HPb59-1 brass include:
- Excellent machinability: Especially suitable for manufacturing precision parts such as pins and screws
- Good wear resistance: Suitable for manufacturing key components such as valve cores and valve seats of valves
- Moderate corrosion resistance: Can meet the requirements of most industrial environments
Key Parts of Brass Valves
The key component construction of brass valves is the cornerstone to ensure their performance and reliability. Before discussing these components, we need to understand the overall design concept of brass valves, това е, through carefully selected materials and ingenious structural arrangements, the valve can be stably operated in various harsh environments.
The core components of brass valves include valve body, valve core, sealing ring and transmission mechanism. Each component plays an irreplaceable role in the normal operation of the valve:
- Valve body: As the skeleton of the entire valve, it is usually cast in high-strength brass. Its internal design has precise flow channels to minimize resistance losses during the flow of the medium. The geometry and wall thickness of the valve body are optimized to balance strength and weight to ensure that it is not too bulky while bearing high pressure.
- Valve core: The heart of the valve determines the control accuracy and response speed of the valve. Taking the brass ball valve as an example, its valve core adopts a spherical design, which can be rotated 90° to achieve the on-off of the medium. The valve core design of modern brass valves is developing towards miniaturization and lightweight. The use of topological optimization and generative design technology not only reduces the inertial mass of the valve core, but also improves its pressure bearing capacity and sealing performance.
- Seal ring: A key component to ensure the sealing of the valve. Common sealing materials include polytetrafluoroethylene (PTFE) and ethylene propylene diene monomer (EPDM). These materials have excellent chemical resistance and temperature resistance, and can maintain good sealing effects under various working conditions. High-end valves also use metal sealing structures, such as bimetallic seals or metal soft seals in copper-sealed gate valves, to meet the challenges of higher temperatures and pressures.
- Transmission mechanism: The power source for opening and closing the valve. Traditional manual operation has gradually been replaced by electric or pneumatic actuators. In particular, the application of direct drive (DDV) servo technology has greatly improved the control accuracy and response speed of the valve. Through closed-loop control and position feedback systems, DDV servo valves can monitor and adjust the valve core position in real time to achieve millimeter-level or even micron-level precise positioning.
Selection Parameters of Brass Valve
When purchasing brass valves, you need to consider several key parameters to ensure that you choose the product that best suits your needs. These parameters not only affect the performance of the valve, but are also directly related to its reliability and service life in actual applications. The following are several of the most important selection parameters:
1. Nominal pressure is the basic parameter for valve selection and reflects the maximum working pressure that the valve can withstand. For brass valves, the nominal pressure range is usually between **PN1.0 and PN16MPa**. When selecting the appropriate nominal pressure level, not only should the working pressure of the pipeline system be considered, but also a certain safety margin should be left to cope with possible pressure fluctuations.
2. Nominal diameter determines the flow capacity of the valve. Brass valves have a wide range of nominal diameters, from **DN15 to DN50** or larger. When selecting the appropriate nominal diameter, you need to balance the flow demand and pressure loss. Too small a diameter may result in greater pressure loss and affect system efficiency; while too large a diameter may cause unnecessary cost waste.
3. Connection method directly affects the convenience of valve installation and maintenance. Common connection methods for brass valves include:
- – Threaded connection: Suitable for small valves, easy to install
- – Flange connection: Suitable for large-diameter valves, easy to disassemble and inspect
- – Welded connection: Provides the highest sealing, but is difficult to install
4. Applicable temperature range is another key parameter. The applicable temperature of brass valves is usually between **-20℃ and +150℃**. Exceeding this range may affect the sealing performance and mechanical strength of the valve. Следователно, when selecting a valve, it is necessary to fully consider the temperature conditions of the working environment to ensure that the valve can maintain stable and reliable performance within the expected temperature range.
В допълнение, it is also necessary to pay attention to parameters such as Sealing form (soft seal or hard seal), Flow characteristics (linear or equal percentage). Although these details may seem small, they may become key factors in determining valve performance in specific applications.
By comprehensively considering these parameters and combining them with specific application requirements, the most suitable brass valve can be selected to ensure that it can meet both functional requirements and achieve ideal economy and reliability in actual use.
