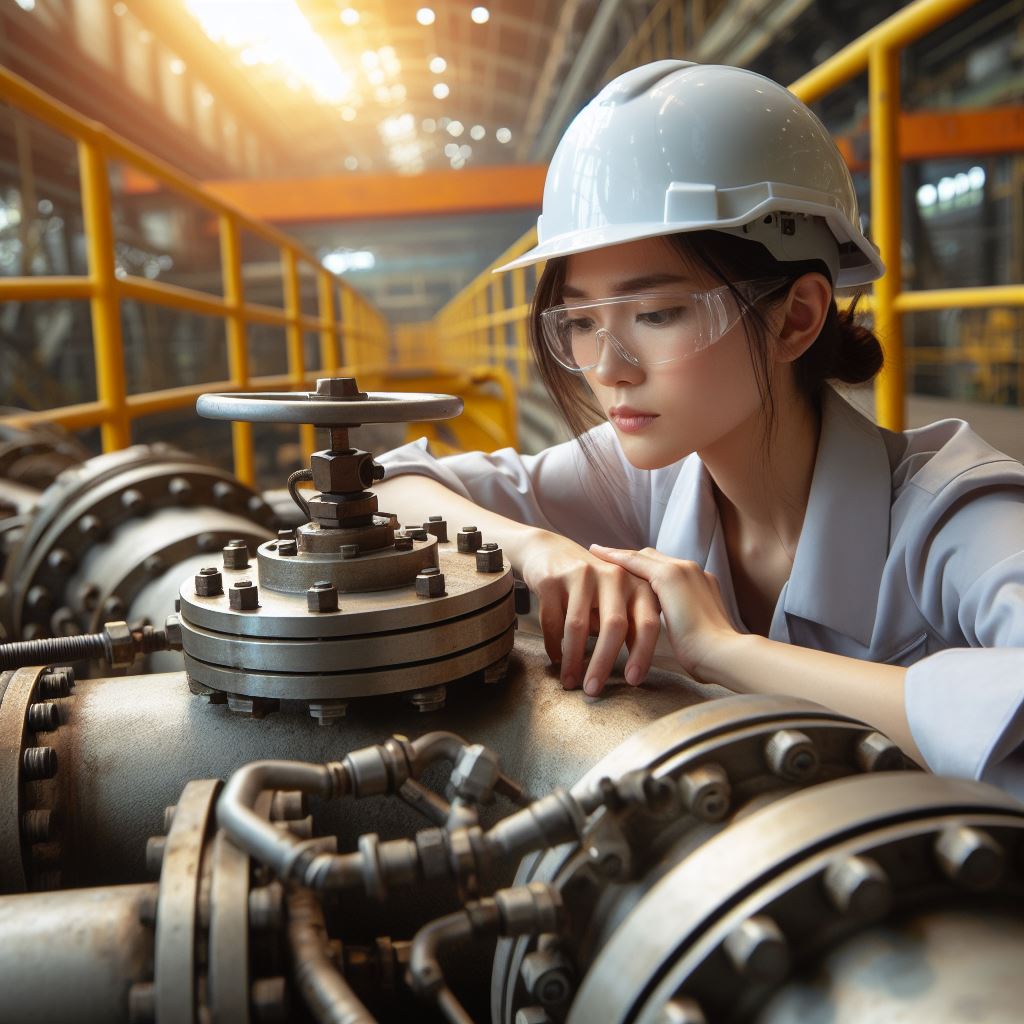
Maintenance Cycle and Procedures
Maintenance Cycle
1.1 The maintenance cycle for valves should be determined by each enterprise based on the characteristics of the production unit, properties of the medium, corrosion rates, and operational cycles.
1.2 The regular inspection of safety valves should adhere to the guidelines outlined in “Regulations for Maintenance and Overhaul of Pressure Vessels.”
Maintenance Procedures
2.1 Clean and inspect the valve body and all valve components thoroughly.
2.2 Replace or repair damaged valve components.
2.3 Grind the sealing surfaces to ensure proper functionality.
2.4 Repair the sealing surfaces of the center flange and end flange.
2.5 Replace or add packing material and change gaskets as necessary.
Maintenance and Quality Standards
Preparation Before Maintenance:
1.1 Gather all relevant technical documentation.
1.2 Ensure availability of tools, gauges, and materials.
1.3 Clean the medium inside the valve thoroughly, meeting safety regulations.
General Guidelines:
2.1 Valves should be tagged with maintenance numbers, working pressure, operating temperature, and medium details.
2.2 Disassembled valve components with directional or positional requirements should be verified or labeled.
2.3 Clean and remove scale from all valve components.
2.4 If non-metallic sealing surfaces are damaged, they should be replaced.
2.5 Select grinding tools and abrasives for sealing surface grinding as per Appendices A, B, and C.
2.6 Bolts and gaskets for temperatures above 250°C should be coated with an anti-seizing agent.
2.7 Anneal copper gaskets before installation.
2.8 Ensure proper installation of bolts. When tightening bolts on center flanges, Absperrschieber, and globe valves should be in the open position.
2.9 Mark the valve body conspicuously after each repair.
Maintenance Quality Standards:
3.1 Valve nameplates should be intact, and safety valve lead seals should be undamaged.
3.2 Castings for valves should be free from defects like cracks, shrinkage holes, and slag inclusions.
3.3 Forged components of valves should have no defects such as delamination, excessive skin, Risse, or blemishes.
3.4 Welded joints on valves should be free from defects like cracks, slag inclusions, porosity, undercut, and poor formation.
3.5 Valve bolts should be fully tightened and free from looseness. All components of the transmission system should be complete and functional.
3.6 Sealing Surfaces:
3.6.1 Check contact surface imprints with a revealing agent.
A. For gate valves, Kugelventile, and check valves, the imprint lines should be continuous, with a width not less than 1mm, uniformly distributed. The limit position of the imprint line on the sealing surface of the gate valve disc should be not less than 3mm from the outer circle (including the imprint line width).
b. The imprint surface of a ball valve should be continuous, with a width not less than the outer diameter of the valve body sealing ring, uniformly distributed.
C. Check the imprints on the contact surface between the steel ring gasket and the sealing groove, and the imprint line should be continuous.
3.6.2 The cumulative thinning after sealing surface repair for safety valves should not exceed 2mm.
3.6.3 The thickness of the welding layer on the sealing surface of ammonia valves should be not less than 2mm.
3.6.4 The roughness of the sealing surface after repair should not be less than Ra1.6, for safety valves not less than Ra0.4.
3.7 Ventilkörper, Valve Cover, and Gaskets:
3.7.1 The connection between the valve seat and the valve body should be firm and leak-free.
3.7.2 The valve disc should have suitable coordination with the guide, with no jamming or derailment at any position.
3.7.3 The maximum mating gap of the raised and depressed flanges on the valve body should meet the requirements in Table 1.
Table 1. Maximum fitting clearance of flange in valve body mm
Valve body middle flange diameter | 42~850 | 90~125 | 130~180 | 185~250 | 255~315 | 320~400 | 405~500 |
maximum gap | 0.40 | 0.45 | 0.50 | 0.55 | 0.65 | 0.75 | 0.80 |
3.7.4 Flange Sealing Surfaces: The flange sealing surfaces should be clean and free from scratches.
3.7.5 Bolt Tightening: For bolts with specified torque requirements, tighten them according to the prescribed torque, and the tightening torque error should not exceed ±5%.
3.7.6 Packing Gland, Packing Seat, and Maximum Fit Clearance: The maximum fit clearance between the packing gland, packing seat, and packing cavity hole should comply with the requirements in Table 2.
Table 2. Maximum fitting clearance between packing gland, bottom sleeve and stuffing box hole mm
Stuffing box hole diameter | 22~26 | 28~34 | 36~44 | 48~70 | 75~106 | 122 |
maximum gap | 0.20 | 0.25 | 0.27 | 0.30 | 0.35 | 0.40 |
3.7.7 The maximum matching clearance between the inner diameter of the packing gland and the valve stem should comply with the requirements in Table 3.
Table 3. Maximum matching clearance between the inner diameter of the packing gland and the valve stem mm
Stem diameter | 14~16 | 18~22 | 24~28 | 32~50 | 55~80 | >90 |
maximum gap | 1.00 | 1.20 | 1.40 | 1.50 | 1.80 | 2.20 |
3.7.8 Packing Gland Condition: Ensure the packing gland is undamaged and free from deformations.
3.8 Operation Components:
3.8.1 Valve Stem and Operation Component Connection: Verify that the connection between the valve stem and the operation component is secure and free from detachment.
3.8.2 Valve Stem End and Valve Disc Connection: Confirm that the connection between the valve stem end and the valve disc is centered within the valve body when the valve is closed.
3.9 Valve Stem:
3.9.1 Valve Stem Surface: Ensure the valve stem surface is free from pits, scratches, and axial grooves. The surface roughness should be Ra1.6.
3.9.2 Valve Stem Straightness: The total straightness tolerance value for the full length of the valve stem should meet the requirements in Table 4.
Table 4. Valve stem full length straightness tolerance value mm
Valve stem total length L | ≤500 | >500~1000 | >1000 |
Straightness tolerance value | Φ0.30 | Φ0.45 | Φ0.60 |
3.9.3 Valve Stem Roundness: The roundness tolerance value for the valve stem should meet the requirements in Table 5.
Table 5. Valve stem roundness tolerance value mm
Stem diameter | roundness tolerance value | Stem diameter | roundness tolerance value |
≤30 | 0.09 | >50~60 | 0.15 |
>30~50 | 0.12 | >60 | 0.18 |
3.9.4 Valve Stem Trapezoidal Thread and Coaxiality: The coaxiality tolerance value between the axis of the trapezoidal thread and the upper sealing conical surface and the valve stem axis should meet the requirements in Table 6.
Table 6. Coaxiality Tolerance Value mm
Valve stem total length L | ≤500 | >500~1000 | >1000 |
Coaxiality tolerance value | 0.15 | 0.30 | 0.45 |
3.9.5 Valve Stem Head: Ensure the valve stem head has no depressions or deformations.
3.9.6 Safety Valve Stem End Spherical Surface: The spherical surface at the end of the safety valve stem should be smooth.
3.9.7 Safety Valve Spring: The surface of the safety valve spring should be free from cracks, and the support planes at both ends of the spring should be perpendicular to the axis.
3.10 Valve Stem Nut:
3.10.1 Fit Clearance: The maximum fit clearance between the valve stem nut’s outer diameter and the support hole should meet the requirements in Table 7.
Table 7. Maximum matching clearance between the outer diameter of the valve stem nut and the bracket hole mm
Stem nut outer diameter | 35~50 | 55~80 | >80 |
Maximum fit clearance | 0.25 | 0.30 | 0.35 |
3.10.2 Handwheel and Bearing Cap: Ensure that the handwheel and bearing cap are not loose.
3.11 Packing Seal:
3.11.1 Packing Alignment: Cut the packing into a 30º bevel, with adjacent turns offset by 120º, and compress each turn gradually.
3.11.2 Packing Compression: After compression, the packing gland should be pressed into the stuffing box by no less than 2mm, and the external leakage part should be no less than 2/3 of the pressing height.
3.11.3 Flexible Operation: After packing, the valve stem should rotate and move up and down smoothly without jamming or leakage.
3.11.4 Packing Selection: Refer to Appendix D (Reference) for the selection of packing.
3.12 Valve Assembly:
3.12.1 Parallel Double Disc Gate Valve: When the valve disc reaches the closed position, the spreading mechanism of the parallel double disc gate valve should rapidly open, aligning with the sealing surface of the valve body. During operation, the double discs should not separate or detach.
3.12.2 Safety Valve Body and Guide Sleeve: The mating of the safety valve body flange and the guide sleeve should be centered.
3.12.3 Position Indicators and Limit Mechanisms: Ensure accurate positioning of position indicators and limit mechanisms.
3.12.4 Drive Mechanism Installation: The installation of the drive mechanism should be flexible, functional, and comply with relevant technical requirements.
Testing and Acceptance
General Requirements
1.1 Prior to installation, the valve should undergo a shell pressure test, seal test, Und, for valves with upper seals, an upper seal test, as determined by the respective specifications.
1.2 For shell pressure tests, upper seal tests, and high-pressure seal tests, the test medium can be air, inert gas, kerosene, Wasser, or a non-corrosive liquid with viscosity not higher than water. For low-pressure seal tests, air or inert gas can be chosen.
1.3 When using water as the test medium, rust inhibitors are allowed. For austenitic stainless steel valves, the chloride content in water should not exceed 25mg/L. Unless specified otherwise, the test medium temperature should be between 5 and 50°C.
1.4 Before valve testing, remove paint and debris from sealing surfaces, and strictly avoid applying leak-proof grease on the sealing surface.
1.5 Valves with bypass valves should undergo shell pressure and seal tests for the bypass valve as well.
1.6 When the test medium is a liquid, air within the valve should be purged. After the valve test, any accumulated liquid inside the valve should be promptly removed.
Valve Shell Pressure Test
2.1 Der test pressure for the valve shell pressure test should be 1.5 times the nominal pressure of the valve.
2.2 The minimum holding time for the valve shell pressure test should be 5 minutes. For liquid test media, there should be no liquid drops or wetness on the outer surface of the shell, and there should be no leakage between the valve body and body liner or between the valve body and bonnet. If the test medium is a gas, leakage should be checked using the specified leak detection method, and there should be no leaks.
2.3 For the jacketed valve, the jacketed portion should undergo a pressure test at 1.5 times the working pressure.
2.4 For Absperrschieber with a nominal pressure less than 1MPa and a nominal diameter greater than or equal to 600mm, shell pressure testing may be omitted and conducted as part of the pipeline system test.
Valve Seal Test
3.1 The valve seal test includes upper seal tests, high-pressure seal tests, and low-pressure seal tests. Seal tests must be conducted after passing the shell pressure test.
3.2 The selection of valve seal test items should be based on diameter and pressure.
3.2.1 For valves with a nominal diameter less than or equal to 100mm and a nominal pressure less than or equal to 25.0MPa, or with a nominal diameter greater than or equal to 125mm and a nominal pressure less than or equal to 10.0MPa, select test items as per Table 8.
Table 8. Valve seal test items 1
Test name | Valve type | |||||
Absperrschieber | Durchgangsventil | Plug Valve | Rückschlagventil | Floating ball valve | Butterfly valve and fixed ball valve | |
Upper seal | Need | Need | No | No | No | No |
Low pressure seal | Need | Choose | Need | Choose | Need | Need |
High pressure seal | Choose | Need | Choose | Need | Choose | Choose |
All valves with upper sealing performance, except for corrugated pipe-sealed valves, should undergo upper seal tests.
For lubricated plug valves, high-pressure seal tests are mandatory, and low-pressure seal tests are optional.
For check valves, low-pressure seal tests can replace high-pressure seal tests.
After high-pressure seal tests on resilient-seated valves, their sealing performance at low pressure may be compromised.
For power-driven medium valves, high-pressure extrusion tests should be conducted at 1.1 times the design pressure difference specified during power-driven device sizing.
3.2.2 For valves with a nominal diameter less than or equal to 100mm and a nominal pressure greater than 25.0MPa, or with a nominal diameter greater than or equal to 125mm and a nominal pressure greater than 10.0MPa, select test items as per Table 9.
Table 9. Valve seal test items 2
Test name | Valve type | |||||
Absperrschieber | Durchgangsventil | Plug Valve | Rückschlagventil | Floating ball valve | Absperrklappe and fixed ball valve | |
Upper seal | Need | Need | No | No | No | No |
Low pressure seal | Choose | Choose | Choose | Choose | Need | Choose |
High pressure seal | Need | Need | Need | Need | Choose | Need |
3.3 The test pressure for high-pressure seal tests and upper seal tests is 1.1 times the nominal pressure of the valve, while the low-pressure seal test pressure is 0.6MPa. The holding time is indicated in Table 10, with the criterion for passing being no leakage.
Table 10. Seal test pressure holding time
Nominal diameter/mm | Holding time/s | ||
Upper seal test | High pressure seal and low pressure seal | ||
Rückschlagventil | Other Valve | ||
≤5065~150200~300≥350 | 156060120 | 606060120 | 1560120120 |
3.4 Gate valves with a nominal pressure less than 1MPa and a nominal diameter greater than or equal to 600mm may omit the separate seal test. Stattdessen, a color imprint method can be used to inspect the sealing surface of the gate.
Safety Valve Adjustment Pressure (Opening Pressure) Test
4.1 The adjustment pressure test for safety valves should include the following items:
4.1.1 Opening pressure.
4.1.2 Reseating pressure.
4.1.3 Repeatability of valve action.
4.1.4 Visual or auditory inspection of valve reseating, checking for jumping, Vibration, sticking, or other harmful vibrations.
4.2 Safety valves should be adjusted according to design requirements. If not specified, the opening pressure should generally be 1.05 Zu 1.1 times the working pressure minus the back pressure, and the reseating pressure should not be less than 0.9 times the working pressure.
4.3 The medium for safety valve adjustment pressure tests can be selected as specified in Table 11.
Table 11. Test medium
working medium | Test medium | working medium | Test medium |
Dampf | saturated vapor | water and other liquids | Wasser |
air and other gases | Luft |
4.4 Safety valve opening and reseating tests should generally be performed at least twice. During the test, the using unit and relevant departments should supervise and confirm on-site. After passing the test, the valve should be lead-sealed, and records of the safety valve adjustment pressure test should be completed and archived by relevant units.
Acceptance
5.1 After the valve test is successful, the interior should be thoroughly cleaned, and protective covers should be added to both ends of the valve.
5.2 For valves such as gate valves, Kugelventile, throttle valves, disk valves, and bottom valves, they should be in the fully closed position. Plug valves and ball valves should be in the fully open position. Diaphragm valves should be in the closed position but not overly tightened to avoid damaging the diaphragm. Check valve discs should be closed and fixed. The sealing surfaces of the closure and valve seat should be coated with industrial rust preventive grease.
5.3 Submit records of the valve pressure test and safety valve adjustment pressure test.
5.4 After valve installation is complete, it should operate with the facility, and all indicators should meet technical standards or production requirements.
5.5 The valve should meet intact standards, and the safety valve lead seal should be qualified.
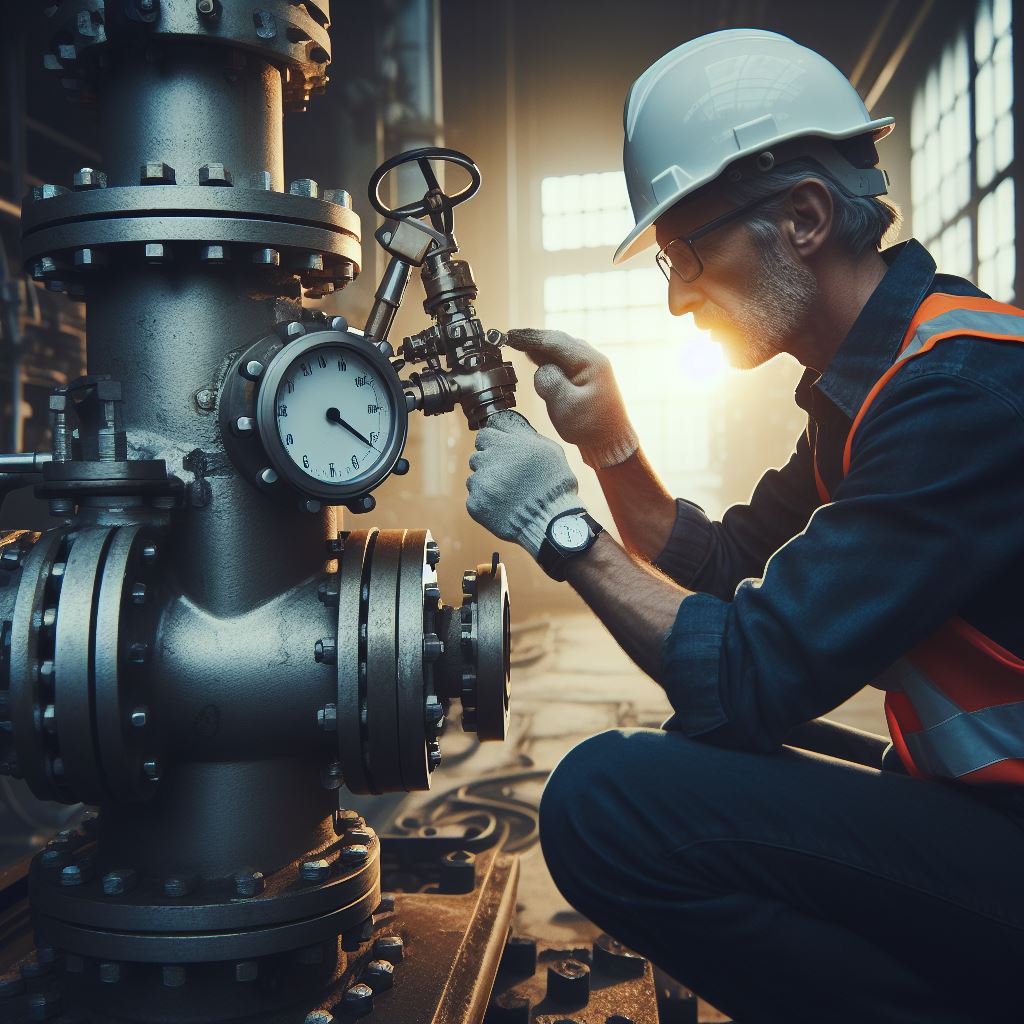
Routinewartung
1.1 Regularly inspect the lubrication of valve oil cups, nozzles, stem threads, and stem nuts. Exposed stem areas should be coated with lubricating grease or protected with covers.
1.2 Periodically check the valve’s seals and fasteners, promptly addressing any leaks or loosening.
1.3 Conduct regular cleaning of the valve’s pneumatic and hydraulic devices.
1.4 Periodically inspect the valve for damage to its anticorrosive coating and insulation layers; any issues found should be repaired promptly.
1.5 Apply rust inhibitor to the threads of flange bolts for protection.
1.6 Promptly replace damaged or lost valve components such as handwheels or handles. Avoid using makeshift tools to prevent damage to the square head at the end of the valve stem.
1.7 For water or steam valves that have been out of use for an extended period, ensure water drainage. If there is sediment accumulation at the valve bottom, open the drain to remove it.
Table 12. Common faults and solutions
Number | Fault Phenomenon | Cause of Issue | Approach |
1 | Valve opening and closing failure | The filling is too tight, the gland is skewed, the opening and closing parts fall off, the valve stem is bent, the valve stem thread is damaged, the closing force of the scaled gate valve is too large, or the valve stem is heated and expands, the bracket bearing is loose and resists the handwheel freezing in cold seasons. | Adjust the tightness of the stuffing box bolts, press the gland correctly, replace the valve, straighten the raft stem, repair the valve stem thread, and remove scale while knocking the valve body flange, while turning the handwheel, re-fix the bearing gland, and use steam to properly heat the valve. |
2 | Packing leakage | The packing gland is loose and the packing is insufficient. The technical performance of the packing is inconsistent. The valve stem is rough, bent, and has axial grooves. | Press the packing gland tightly, increase the packing, replace the packing, improve the surface finish, straighten the valve stem, and repair the grooves. |
3 | Middle flange leakage | The flange bolts are unevenly tightened and the technical performance of the gasket is inconsistent. The flange sealing surface is defective. | The bolt torque should be consistent, replace the gasket, repair the sealing surface |
4 | Valve internal leakage | Foreign matter falls into the valve, and the sealing surface sticks to the foreign matter. The spherical surface of the valve stem end is deformed or the expansion mechanism of the suspended double gate valve is worn and the sealing surface is damaged. | Remove foreign matter, repair the spherical surface, repair the expansion mechanism, and train |