As a valve expert with years of experience in industrial applications, I often emphasize the importance of incorporating check valves on the discharge side of pumps. This critical valve plays a vital role in ensuring efficient and safe pump operation, while also protecting the system from potential damage.
In dit artikel, we’ll explore the reasons why terugslagkleppen are essential components in pump installations and the benefits they provide. Understanding the significance of these valves can help you make informed decisions and implement best practices for your pumping systems.
What is a Check Valve?
A check valve is a specialized valve designed to allow flow in one direction while preventing backflow or reverse flow in the opposite direction. This valve operates automatically, opening to permit forward flow and closing to block any reverse flow, making it an essential component in various fluid handling systems.
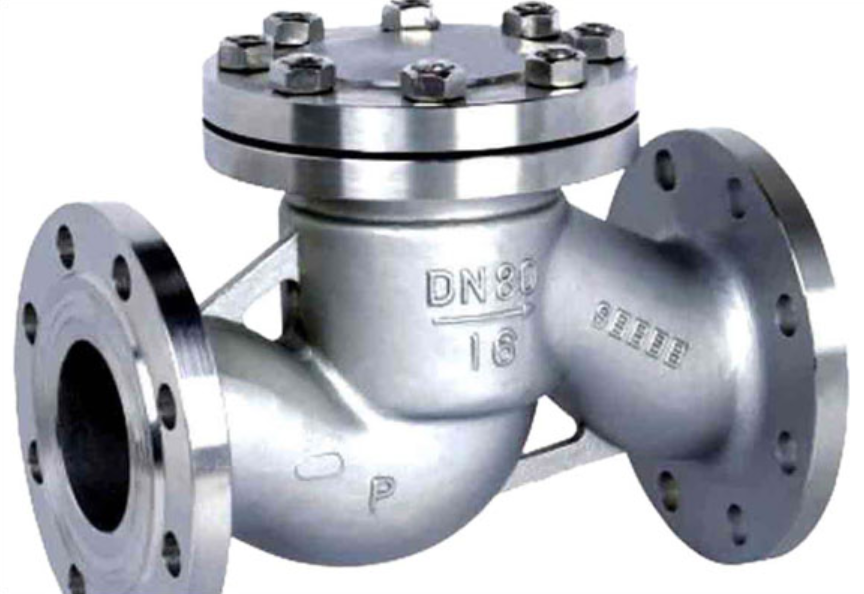
Why are Check Valves Required on Pump Discharges?
- Preventing Reverse Flow and Pump Damage
When a pump is stopped or shut down, the fluid in the discharge line can potentially flow back toward the pump due to gravity or system pressure. This reverse flow can cause damage to the pump’s internal components, such as the impeller, shaft, and bearings. By installing a check valve on the pump discharge, you can effectively prevent this reverse flow, protecting the pump from potential damage and extending its service life. - Systeemdruk handhaven
In systems with multiple pumps or where the discharge line connects to a pressurized system, a check valve on the pump discharge helps maintain the desired system pressure. Without a check valve, the fluid could flow back through the idle pump, causing a loss of pressure and potentially disrupting the overall system operation. - Preventing Pump Rotation in the Reverse Direction
In sommige gevallen, the reverse flow of fluid can cause the pump’s impeller to rotate in the opposite direction. This undesirable phenomenon, bekend als “pump spin-back,” can lead to damage, increased wear, and potential failure of the pump components. Installing a check valve on the discharge side effectively prevents pump spin-back, ensuring the pump operates as intended. - Reducing Water Hammer
Water hammer, a phenomenon characterized by sudden pressure surges in piping systems, can occur when a pump is stopped abruptly, causing the fluid to reverse direction and slam against the closed valve or pump components. By installing a check valve on the pump discharge, you can mitigate the effects of water hammer, reducing the risk of damage to the piping system and associated equipment.
Types of Check Valves Suitable for Pump Discharges
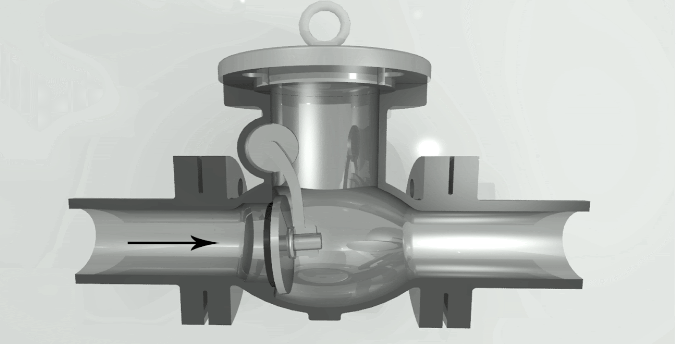
Various types of check valves can be used on pump discharges, depending on the specific application and operating conditions. Some common options include:
- Swing Check Valves
- Lift Check Valves
- Kogelterugslagkleppen
- Split Disc Check Valves
- Spring-Loaded Check Valves
When selecting a check valve for your pump discharge, it’s crucial to consider factors such as flow rate, druk, temperatuur, and the characteristics of the fluid being handled. Consulting with valve experts and following industry best practices can ensure the optimal selection and installation of check valves for your pumping systems.
By incorporating check valves on pump discharges, you can safeguard your equipment, extend its service life, and maintain efficient and reliable system operation. Prioritizing the installation of these critical valves is a best practice widely recommended by valve experts and industry professionals alike.