One-way valves also called check valves or non-return valves. It is a valve where the fluid can only flow along the inlet and the medium at the outlet cannot flow back.
It use in hydraulic systems to prevent the reverse flow of oil, or in pneumatic systems to prevent the reverse flow of compressed air. They play a crucial role in various industries by ensuring the unidirectional flow of substances in pipelines, systems, and equipment, thereby enhancing safety, efficiency, and performance.
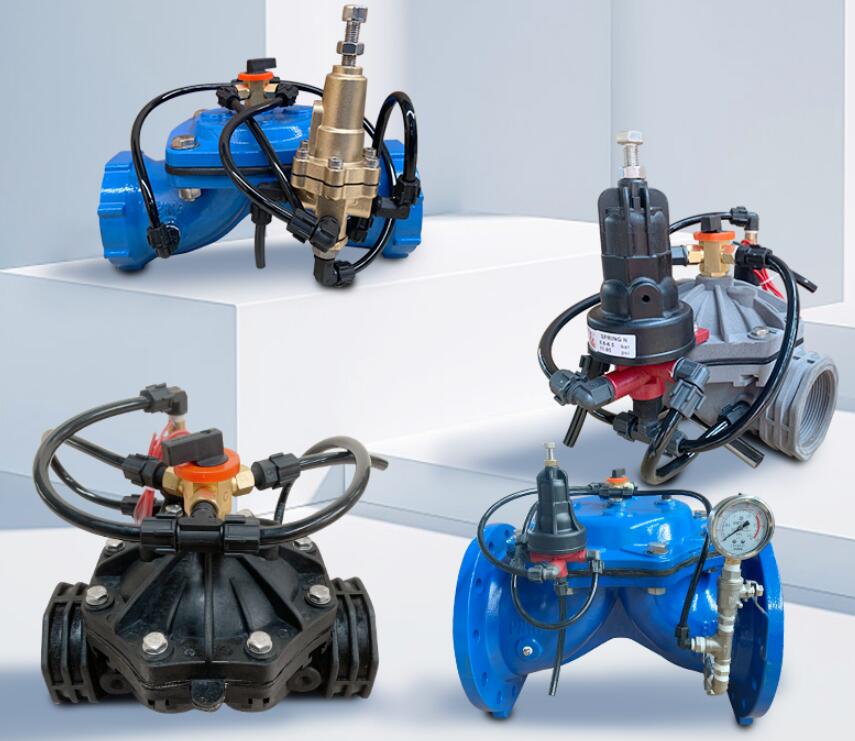
One way valves has straight-through and right-angle type two
Straight-through one way type
with a threaded connection installed in the pipeline.
A straight-through one-way valve is a type of valve that allows fluid or gas to flow in only one direction while preventing reverse flow. It features a straight-through design, facilitating unobstructed flow passage for enhanced efficiency and minimal pressure drop. This valve is commonly used in applications where maintaining directional flow is critical, such as in plumbing systems, irrigation, and industrial processes.
Right-angle one way type has three forms
threaded connection, welded connection and flange connection.
A right-angle one-way valve is a type of valve designed to regulate the flow of fluid or gas in a single direction while preventing backflow. It features an L-shaped or right-angle configuration, allowing for installation in tight spaces or where a perpendicular connection is required. This valve is commonly used in various industries, including automotive, medical devices, and HVAC systems, where space constraints or specific installation requirements exist.
One Way Valve Types
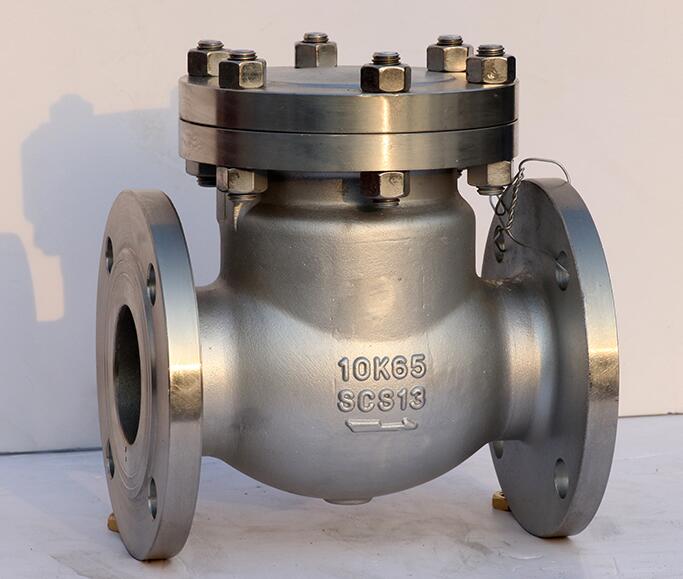
Classification Based on Design and Mechanism
Check valve types are: spring type, gravity type, swing type, plastic diaphragm type. According to the structure: lift check valves, butterfly check valves, swing check valves, ball check valve and flap check valve.
- Lifting check valve: Divided into vertical check, horizontal check.
- Swing check valve: Divided into single-valve check, double check valves, multi-flap check.
- Ball Check Valves: Ball check valves are mechanical devices used to control the flow of fluids or gases in pipelines by allowing flow in one direction while preventing backflow in the opposite direction. They consist of a spherical ball inside a valve body, which moves freely to allow flow when the pressure on the inlet side is higher than the outlet side. When flow reverses, the ball moves to block the passage, preventing backflow.
- Flap Check Valves: Flap check valves are mechanical devices designed to regulate fluid or gas flow in pipelines by permitting flow in one direction while preventing backflow in the opposite direction. They feature a hinged flap or disc that opens in the direction of flow and closes to block reverse flow. This design allows for efficient flow control, preventing the reversal of fluid or gas and ensuring the integrity of the pipeline system. Flap check valves are widely used in diverse industries due to their reliability, low maintenance requirements, and effectiveness in preventing backflow.
Check valves according to the connection form: threaded check type, welded check type, flange check type.
Classification Based on Application
Medium type | Recommended materials |
Corrosive liquids | Stainless steel, alloy steel |
Strong acids and alkalis | PTFE (polytetrafluoroethylene) |
High-temperature steam | Special heat-resistant alloys |
- Hydraulic check valves are essential components in hydraulic systems, designed to control the flow of fluid in one direction while preventing reverse flow. They utilize internal mechanisms such as spring-loaded discs or poppets to allow fluid to flow in one direction, while automatically closing to block flow in the opposite direction. These valves ensure the integrity and efficiency of hydraulic systems by preventing fluid backflow, which could cause damage or malfunction.
- Pneumatic check valves are devices used in pneumatic systems to regulate the flow of compressed air or gases in one direction while preventing reverse flow. They operate using internal mechanisms such as spring-loaded discs or poppets, which open to allow airflow in one direction and close to block airflow in the opposite direction. These valves ensure the proper functioning of pneumatic systems by preventing backflow, which could disrupt operations or damage equipment.
- Medical check valves are specialized components used in medical devices and equipment to control the flow of fluids or gases in one direction while preventing backflow. These valves are crucial for maintaining the integrity of medical systems, ensuring proper delivery of medications, gases, or fluids to patients during procedures or treatments. They operate using mechanisms like ball, diaphragm, or spring-loaded designs to allow flow in one direction while blocking flow in the opposite direction.
- Duckbill valves are one-way passive check valves designed to allow fluid or gas flow in one direction while preventing backflow. Their unique shape resembles a duck’s bill, hence the name. These valves consist of a flexible elastomeric material, such as silicone or rubber, formed into a tapered shape that naturally stays closed when no pressure is applied. When fluid or gas flows in the desired direction, the pressure opens the valve, allowing passage. However, when the flow stops or reverses, the valve’s elasticity causes it to close, preventing backflow. Duckbill valves find applications in various industries, including medical devices, wastewater treatment, automotive, and aerospace, where reliable one-way flow control is essential.
- Pressure relief valves are safety devices used to protect equipment or systems from excessive pressure buildup by automatically opening to release excess pressure. They operate by sensing the pressure in a system and, when it exceeds a predetermined threshold, they open to allow the release of fluid or gas, thereby preventing damage or catastrophic failure. Pressure relief valves are crucial components in various industries, including oil and gas, chemical processing, power generation, and water treatment, where maintaining safe operating pressures is essential. They come in different designs, including spring-loaded, pilot-operated, and balanced bellows, each suitable for specific applications and pressure ranges.
Ordinary check type
Ordinary check structures allow fluid flow in only one direction. Forward opening pressure is generally 0.03-0.05Mpa.
The main applications of ordinary one-way valves:
- The valve usually installed at the outlet of the pump. Because the pressure shock will affect the normal operation of the pump. And it prevents the pump does not work when the system oil backflow.
- One-way valves are also capable of operating in separate high and low pressure chambers.
- The types of one-way valves are: one-way throttle valves, one-way pressure reducing valves, one-way sequence valves.
- In the backpressure valves, check valves installs the return path.
Straight-through type
Straight-through check valves in the direction of oil flow and the direction of the axis of the valve is the same.
Pipe connection valves, the oil port of such valve can be connected to the oil pipe through the pipe connector. The weight of its valve body depends on the pipe support, so the volume of the valve can not be too large and too heavy.
Right-angle one way valves
The axis of the inlet and outlet of the right-angle check valves are perpendicular to the axis of the valve body.
Selection considerations
When selecting a check valve, several key factors need to be considered to ensure optimal performance and reliability in a specific application. These factors include operating pressure, flow requirements, media characteristics, temperature range, and material selection. The details are as follows:
- Working pressure is the basis for selection. The working pressure of the check valve should match the maximum working pressure of the system to ensure that the valve can maintain a stable seal under high pressure. For example, in high-pressure water jet cutting equipment, the working pressure of the check valve must reach hundreds of MPa to prevent the reverse flow of high-pressure water.
- Flow requirements directly affect the size and response speed of the valve. Improper selection may result in pressure loss or response delay. For large flow applications, such as large hydraulic systems, it may be necessary to select a specially designed large flow hydraulically controlled check valve with a nominal flow of more than 1000L/min.
- Consideration of media characteristics is particularly important. Different media have different requirements for valve materials and seals: list 1
- Temperature range is another key parameter. The choice of valve materials and seals needs to take into account the operating temperature to ensure that they can maintain good performance under extreme conditions. For example, some special check valves can operate in an extremely wide temperature range of -196°C to +850°C[1].
- In addition, mounting method and maintenance convenience need to be considered. The choice of threaded connection, flange connection or welding should match the system interface. The replaceability of wearing parts will also affect the long-term operating cost.
Installation considerations
During the installation of the check valve, in addition to the choice of direction and position, there are some key considerations that require special attention to ensure that the valve can work properly and maximize its performance. These considerations are as follows:
1.Sealing check : After installation, a comprehensive sealing check should be performed on the connection between the check valve and the pipeline. This can be done by applying soapy water or a special leak detection fluid to observe whether there are bubbles or abnormal leaks. For high-pressure systems, it may be necessary to use professional pressure testing equipment to verify the sealing performance.
2.Vibration control : In some applications, the check valve may produce significant vibration. To reduce this vibration, the following measures can be taken:
- Use flexible connectors or vibration dampers to connect the check valve and the pipeline system
- Install a damper or muffler near the check valve
- Adjust the spring preload of the check valve as needed
3.Bypass installation : In some critical systems, it is recommended to install a manual bypass valve next to the check valve. The benefits of doing so include:
- Convenient emergency operation
- When the check valve needs to be repaired or replaced, the entire system can be operated without stopping
- Improving the overall reliability and safety of the system
4.Pipeline support: For large or heavy check valves, sufficient pipeline support should be provided near the installation location. Reasonable support can not only reduce the stress on the check valve, but also reduce the vibration of the pipeline system, thereby improving the stability and life of the entire system.
5.Electrical connection: For check valves with electrical control functions (such as electric check valves), the following points should be noted:
- Install lightning protection and surge protection devices when necessary
- Make sure that the electrical connection meets the relevant safety standards
- Use cables and connectors of appropriate specifications
Description of Emerging Trends and Innovations of one way valve
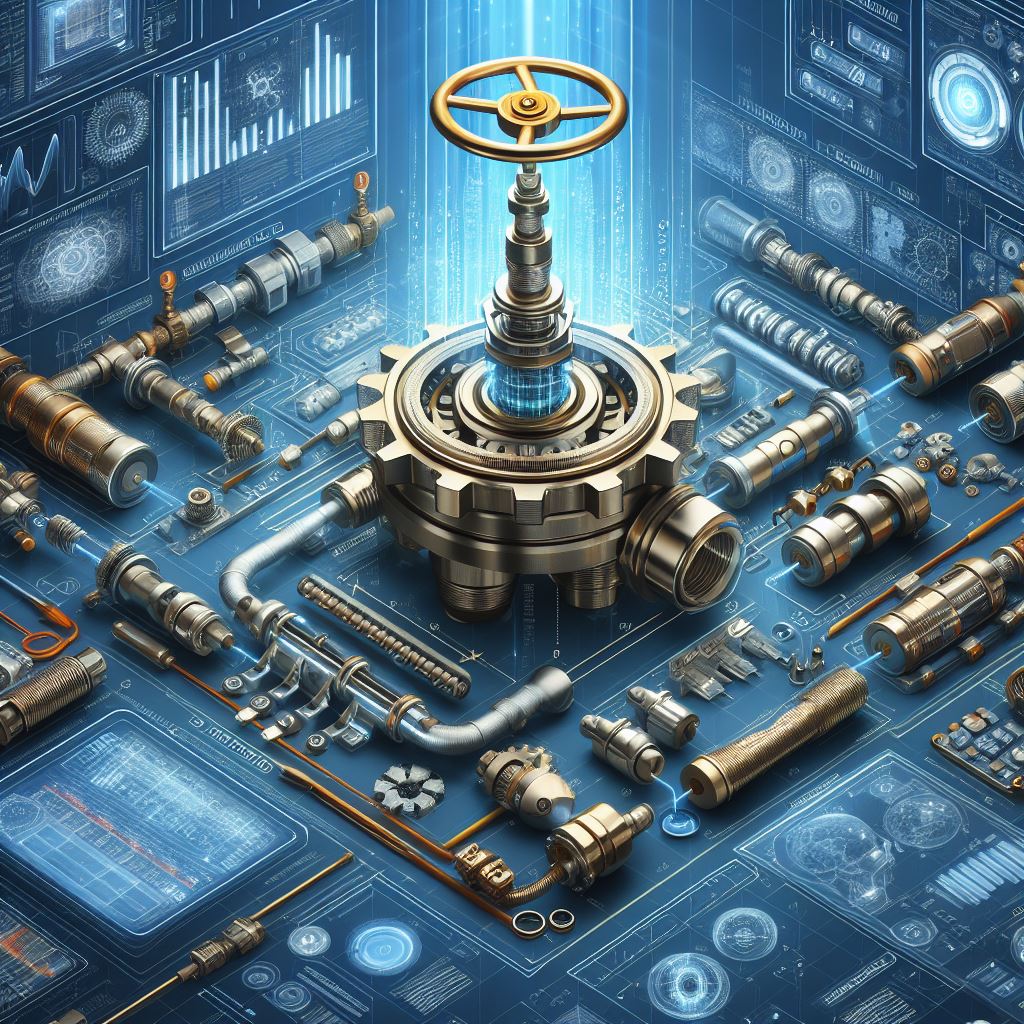
The emerging trends and innovations in one-way valve technology signify a transformative phase in fluid control mechanisms. These advancements are characterized by a shift towards smarter, more efficient, and environmentally sustainable solutions.
- Smart Valve Technologies:
- Integration of sensors and actuators for real-time monitoring and control.
- Implementation of predictive maintenance algorithms for proactive servicing.
- Sustainable Materials:
- Adoption of eco-friendly materials such as bio-based polymers and recyclable metals.
- Development of valves with reduced environmental footprint and improved lifecycle.
- Integration with IoT:
- Connectivity with Internet of Things (IoT) platforms for remote operation and data analytics.
- Utilization of cloud-based solutions for centralized management and optimization.
- Performance Enhancements:
- Enhanced flow control capabilities for precise regulation of fluid flow.
- Reduction of pressure drop and energy consumption through innovative designs.
- Adaptation to Industry Needs:
- Customization of valve designs to meet specific industry requirements and applications.
- Tailored solutions for challenging environments such as high-pressure or corrosive conditions.
These emerging trends and innovations reflect the industry’s commitment to efficiency, sustainability, and technological advancement, paving the way for a new era of fluid control solutions.