Flanged cast steel gate valve, known as “flange connection API cast steel gate valve”, it can be applied to ANSI class 150~2500, working temperature <600℃, petroleum, хімічний, thermal power station and other working conditions of the pipeline.
Flanged cast steel gate valve for media: води, масло, пара, etc and operation methods are: manual, gear drive, електричний, пневматичний, тощо.
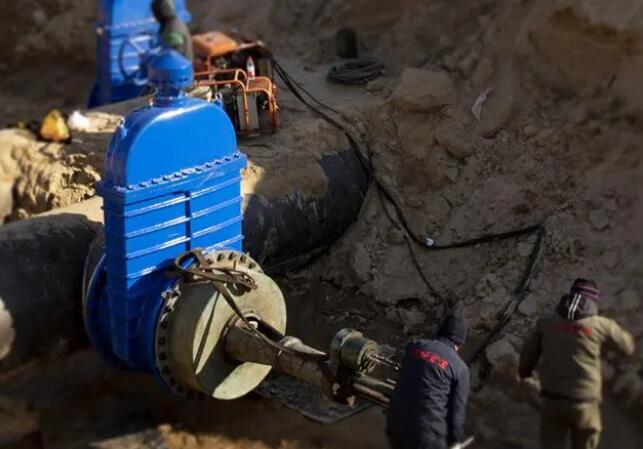
Flanged cast steel gate valve installation requirements:
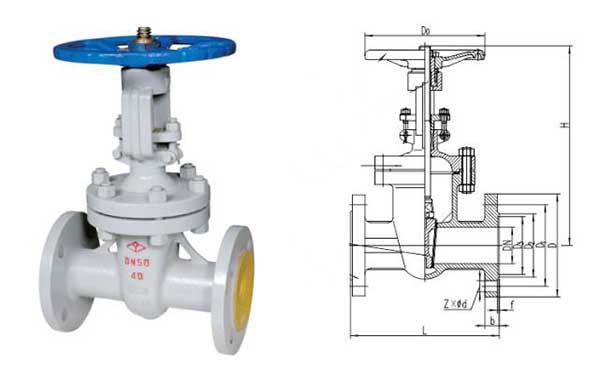
1.Before installation, please check the inside of the valve cavity and sealing surface, and make sure there is no dust or sand adhering.
2.The bolts of each connection must be tightened evenly.
3.To ensure the sealing of the packing and to ensure the flexible opening of the gate, the packing part must be tightly pressed.
4.Before installing the valve, check the valve type, connection size and pay attention to the flow direction of the medium to ensure consistency with the valve requirements.
5.When installing the valve, the space required to drive the valve must be ensured.
6.The wiring of the driving device should be done in accordance with the wiring diagram.
7.The gate valve must be regularly maintained and not allowed to collide or squeeze so as not to affect the seal.
Flanged cast steel gate valve maintenance requirements:

The valve cleaning:
clean the general media with water can be. If the cleaning is harmful to health media, please understand its characteristics, and then choose the appropriate cleaning method.
Valve disassembly:
Before rusting, protect the processing surface of the valve seat, spool, stem and push rod and other precision parts, and then rusty parts of the exposed surface for rust removal treatment.
Valve seat:
if the seal surface rust and wear is small can be processed through mechanical processing, if serious damage, should be replaced with a new one. Проте, after repair or replacement, regardless of the hard seal surface, must be polished and smoothed.
Valve stem:
the surface has been damaged can only be replaced with a new one.
Push rod:
guide device and sealing surface damage: the reverse-acting actuator needs to be replaced with a new actuator, the positive actuator can be repaired and used.
Compression spring:
If there is a defect that affects the strength (such as cracks), it must be replaced.
Damageable parts:
Упаковка, gasket and O-ring. All parts need to be replaced every time you check them. Spool and diaphragm should also be inspected to prevent future cracks, signs of aging and corrosion, after inspection to decide whether to replace, but the diaphragm life is usually 2-3 роки.
Valve assembly pay attention to alignment:
Tighten the bolts on the diagonal, and then add lubricant to the sliding parts. After assembly, the product should be commissioned according to the factory test items and methods, and the compression force of the packing and the closing position of the spool can be adjusted during this period.